Undoubtedly, the turbulent economic conditions of the previous five years forced businesses of all sizes to cut their budgets and search for more efficient methods of operation, but the fact is that every company can gain from routine supply chain reviews. Even bigger benefits come from a commitment to ongoing improvement.
By incorporating audits and efficiency reporting into the heart of your business processes, you can:
- Get rid of waste and pointless redo.
- Identify continuing cost reductions.
- Make sure that no possible issue is given more time than necessary to go unnoticed.
- Encourage employees to take more ownership and responsibility for their work.
Although the advantages are appealing, more work needs to be done to create a fully operational system that eliminates waste and continuously incorporates small modifications.
Although the advantages are alluring, a fully operational system that eliminates waste and keeps adding small adjustments to increase your supply chain’s efficiency still requires a lot of work.
We’ve listed eight spots where you can start an efficiency drive for your company using our vast industry experience.
Before we Start:
You must first choose whether this will be a one-time evaluation to eliminate waste or a comprehensive commitment to end-to-end supply chain efficiency growth.
The latter is what we advise because it uses fewer resources and costs less money over time. However, some businesses won’t be able to allocate the funds necessary for a thorough redesign. If this is the case for your company, conducting a single assessment that includes even a small number of these suggestions will likely be beneficial and build the foundation for other projects in the future.
Get support from all organizational levels if your company is in a position to commit to a continuous improvement program. Communication must be as fluid as the supply chain procedures you will streamline, from the managers who will be responsible for driving the change to the employees who will provide the essential feedback.
How to Improve Supply Chain Efficiency And Cut Waste?
- Consider the Product Design
Examining and reevaluating the design of your items is one technique to optimize your manufacturing while also decreasing waste. Determine any opportunities or strategies for cutting back on the utilization of raw materials or for substituting less expensive materials. If you can reduce tiny expenses, you might be able to make significant savings.
Additionally, consider your product packaging choices and look for opportunities to employ less expensive materials.
- Control resources
In addition to simply looking at using less expensive resources, you should look at each of your production processes to see which ones are causing waste. Processes that produce waste that isn’t recyclable or usable should be redesigned. Even recyclable garbage should be evaluated, and recycling costs should be taken into account. The cost of making changes may seem high when processes are being optimized, but over time, the cost of waste, management, disposal, and even recycling can pile up.
- Choose the Proper Equipment
Having the proper waste management equipment can help with garbage handling and disposal, saving time, money, and a lot of difficulties. Technology and tools for waste management have advanced significantly. Trash compactors help you manage garbage more effectively and save a lot of money in the long run.
To begin, it’s crucial to understand how much and what kind of waste your supply chain generates. There are several options available, some of which have very specific applications that you could find useful.
- Raising Production Standards
While quality management should aim to reduce the waste of raw materials, quality control frequently concentrates on finished goods. Increasing the number of products that pass quality control may be a double benefit of streamlining your manufacturing operations to reduce total waste.
- Employee Evaluation
The workers tasked with manufacturing will likely have a better understanding of where trash is produced and the difficulties in handling it. They could also offer a lot of advice on how to improve trash management and decrease waste as much as possible. Since this type of cooperative approach typically produces successful outcomes, you can set up focus groups charged with locating and optimizing waste.
- Inventory Control
You can get closer to a perfect-order measurement of 100% by using lean strategies like JIT (Just-in-time) logistics. In addition to lowering order errors, it can also significantly lower a number of inventory management expenses like warehousing, electricity costs, rental prices, and even insurance and taxes. Weigh the benefits and drawbacks carefully before placing repeated orders because doing so may raise transport costs and result in greater vendor fees if each item has a smaller value.
Author Bio:
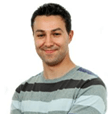
Erich Lawson is passionate about saving the environment through effective recycling techniques and modern innovations. He works with Compactor Management Company and writes on a variety of topics related to recycling, including tips and advice on how balers, compactors, and shredders can be used to reduce industrial waste. He loves helping businesses understand how to lower their monthly garbage bills and increase revenue from recycling.
This post is Sponsored Content